Tubing is available in a wide array of sizes, materials, lengths, and origins. One of the key factors that must be considered when selecting tubing is the manufacturing process: Seamless or Welded.
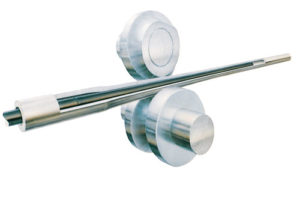
Seamless Manufacturing Process
Seamless tubing is manufactured from a solid billet that has been extruded into a seamless pipe, known as a hollow or mother tube. That pipe is then reduced to smaller sizes using pilgering and/or cold drawing. Pilgering, also known as cold rolling, uses two rollers with grooves to control the OD reduction and a mandrel to control the ID reduction. Pilgering is very fast and can reduce cross sections by as much as 90%, but has limitations on smaller OD tubing and is typically best suited for high volume manufacturing due to the difficult change-out.
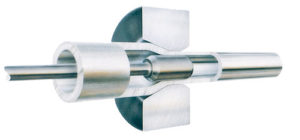
Cold drawing involves crushing one end of the hollow to insert it through a die, then drawing it through the die to reduce the diameter of the tube. The inside of the tube can be controlled using a rod (known as rod drawing), a plug (known as plug drawing), or no internal support (known as sinking). Cold drawing is well suited for small diameter tubing, custom size tubing, and smaller production runs of tubing.
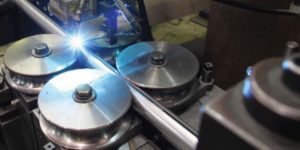
Welded Manufacturing Process
Welded tubing is manufactured using flat strip that is roll formed into a circular cross section and then longitudinally welded using TIG welding or Laser Welding processes. After welding, the weld seam, or bead, can be left as is (“as welded”), or it can be refined by cold working the bead using rolling and forging methods. The welded tubing can also be drawn after welding, just like seamless tubing, which results in an even finer weld seam, tighter tolerances, and better surface finish.
Comparison
- PRICE: Welded tubing is typically much cheaper than seamless tubing. This is due to the simpler manufacturing process used in welded tubing vs. seamless tubing. However, seamless tubing can require smaller manufacturing runs, so a custom size may be cheaper in seamless because less quantity is required than producing a custom size of welded tubing.
- LEAD TIME: For standard sizes, welded and seamless tubing have similar lead times and are often available in stock.
- THIN WALLS: Welded tubing is typically easier to produce in thinner wall sizes than seamless. Larger diameter tubing with thin walls is very difficult to produce in seamless, while it is very available in welded.
- HEAVY WALLS: Heavy walls are generally more easily achieved with seamless tubing. Seamless tubing is often preferred for heavy wall tubing since heavy walls are generally for high pressure applications.
- CUSTOM SIZES: For non-standard, custom sizes, seamless tubing is typically more economical and has a quicker delivery.
- CORROSION RESISTANCE: Seamless tubing is generally considered to be the most consistent material with the least impurities, which results in a higher corrosion resistance. Welded tubing can have impurities near the weld seam that causes it to be more susceptible to corrosion. However, major US welded tube manufacturers have developed technology and methods for producing extremely high purity and consistent weld seams.
- PRESSURE RATING: There is some debate over this as some would consider seamless and welded tubing to have the same pressure rating, while others argue that the welded tubing should be rated at 80% of the capacity of seamless. The 80% value is based on the view of the weld being a cast material, and cast materials have a lower rating. However, others argue that welded material with the right non-destructive testing (NDT) can be proven to match the same pressure rating as seamless tubing. NDT would include eddy current, ultrasonic, and/or radiographic testing. Ultimately, if there is a concern over the rating of welded tubing, it can be pressure tested at the manufacturer or by a third party to confirm the actual pressure retaining capability of the tubing.
Conclusion
Despite what some would argue, there is not always a clear cut answer to which tube is always better. The application, the purchaser’s specifications, and the manufacturer’s capabilities should all be taken into account when making a decision. For certain sizes or cost limitations, there may only be one option. But when considering quality, all aspects of the application and the specific manufacturer’s capability must be considered. Tubing Central stocks seamless and welded tubing from the highest quality manufacturers only. Fully traceable physical and chemical test reports are available for all tubing, and additional testing, cleaning, and inspection can be performed on any tubing to meet each customer’s specific requirements.
Image Sources:
http://www.mannesmann-stainless-tubes.com/english/process/process-fundamentals/process-fundamentals.html
https://www.thefabricator.com/article/tubepipeproduction/tube-producer-opens-doors-to-new-markets-controls-costs-with-laser-welding